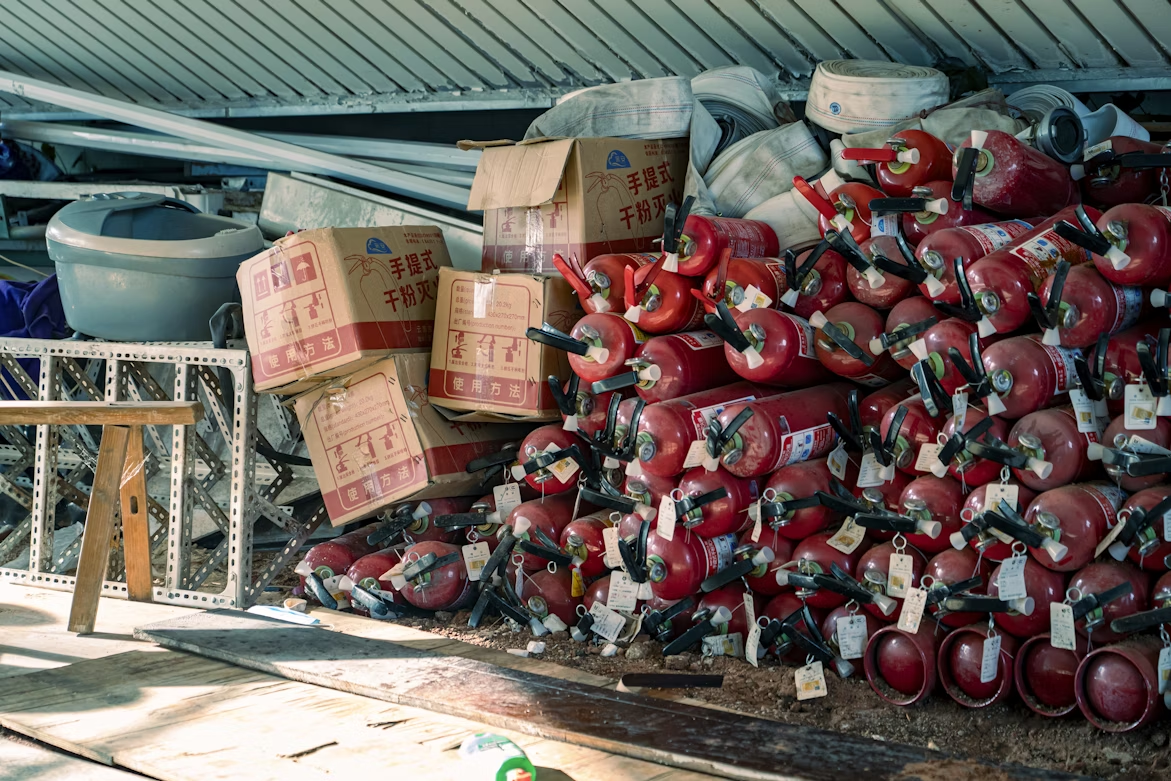
In today’s globalized economy, supply chains play a crucial role in ensuring businesses operate smoothly. However, critical materials supply chains often face significant challenges, one of which is the presence of bottlenecks. A bottleneck occurs when the flow of goods or materials is restricted, leading to delays and inefficiencies. These disruptions can be especially detrimental when dealing with critical materials, which are essential for the production of goods in various industries.
Overcoming bottlenecks in critical materials supply chains requires strategic solutions that address both short-term obstacles and long-term systemic issues. In this article, we will examine key strategies that businesses can employ to minimize or eliminate bottlenecks and enhance the efficiency of their supply chains.
Identifying Bottlenecks in Critical Materials Supply Chains
The first step in overcoming bottlenecks is identifying where they occur in the supply chain. Bottlenecks can occur at various stages, including production, transportation, or inventory management. A common bottleneck in critical materials supply chains is the procurement of raw materials. Delays in sourcing essential components or the inability to secure sufficient inventory can severely impact production timelines.
To pinpoint bottlenecks, companies should conduct a thorough supply chain analysis, focusing on the flow of critical materials and identifying any points where delays or disruptions are consistently occurring. Key performance indicators (KPIs), such as lead time, inventory turnover, and order fulfillment rates, can aid in this process.
Collaborative Supplier Relationships for Improved Coordination
One of the most effective ways to mitigate bottlenecks is to strengthen relationships with suppliers. By fostering collaboration, businesses can create more transparent and efficient procurement processes. Regular communication with suppliers ensures they are aware of production schedules, allowing for proactive planning to address any potential delays in material delivery.
Long-term supplier partnerships can also help companies better forecast demand and align their production schedules with material availability. With a well-coordinated approach, suppliers can better anticipate and meet the company’s needs, thereby reducing the risk of bottlenecks caused by material shortages.
Technology Integration for Real-Time Data Access
Another strategic solution to supply chain bottlenecks is the integration of advanced technologies. Real-time data is crucial for monitoring the movement of critical materials across the supply chain. Implementing technologies such as Internet of Things (IoT) sensors, automated tracking systems, and artificial intelligence (AI) can provide businesses with up-to-the-minute information on inventory levels, order status, and transportation delays.
By leveraging data analytics, companies can predict and manage supply chain disruptions before they turn into significant bottlenecks. For instance, AI-driven predictive analytics can analyze historical data to forecast potential material shortages, allowing companies to adjust procurement strategies and prevent delays. Real-time visibility also enables businesses to make quicker, more informed decisions, ultimately improving overall supply chain efficiency.
Streamlining Transportation and Logistics
Transportation is often a significant source of bottlenecks, particularly when dealing with critical materials that are sourced globally. Delays in shipping, port congestion, and unpredictable transportation costs can all create significant roadblocks in the supply chain.
To address these issues, businesses can optimize their transportation networks by diversifying shipping routes, investing in faster transportation methods, or working with third-party logistics (3PL) providers who specialize in handling critical materials. Additionally, improving coordination with freight carriers and utilizing technology to track shipments in real time can help companies better anticipate delays and find alternative solutions more quickly.
Optimizing Inventory Management
An efficient inventory management system is crucial in overcoming bottlenecks in critical materials supply chains. When companies do not have sufficient inventory on hand to meet demand or when they hold excessive stock, they can experience delays or disruptions in their operations.
To optimize inventory management, businesses should adopt just-in-time (JIT) inventory systems, which help to reduce excess stock while ensuring materials arrive precisely when needed. Additionally, implementing automated inventory management systems can improve tracking, minimize human error, and provide more accurate data on stock levels.
Maintaining a buffer stock of critical materials can also provide a safety net during unexpected disruptions, ensuring that production continues uninterrupted. The key is finding the right balance between maintaining adequate stock and avoiding overstocking, which ties up valuable resources.
Enhancing Risk Management and Contingency Planning
Finally, to prevent supply chain bottlenecks, businesses should implement robust risk management strategies and contingency plans. Critical materials supply chains are vulnerable to disruptions from a wide range of sources, including natural disasters, geopolitical events, and supply shortages. By conducting thorough risk assessments, companies can identify potential threats and develop strategies to mitigate their impact.
Contingency planning should include alternative sourcing strategies, emergency transportation plans, and the establishment of backup suppliers or inventory storage facilities to ensure continuity of operations. In the event of a disruption, businesses can pivot quickly to minimize the impact on production and delivery timelines.
Overcoming bottlenecks in the critical materials supply chain requires a combination of strategic planning, technology integration, and strong supplier relationships. By identifying potential bottlenecks, fostering collaboration, and implementing technology solutions, businesses can create a more resilient and efficient supply chain. Furthermore, effective inventory management, risk management, and contingency planning will help minimize disruptions, ensuring that critical materials flow smoothly and reducing the likelihood of production delays.